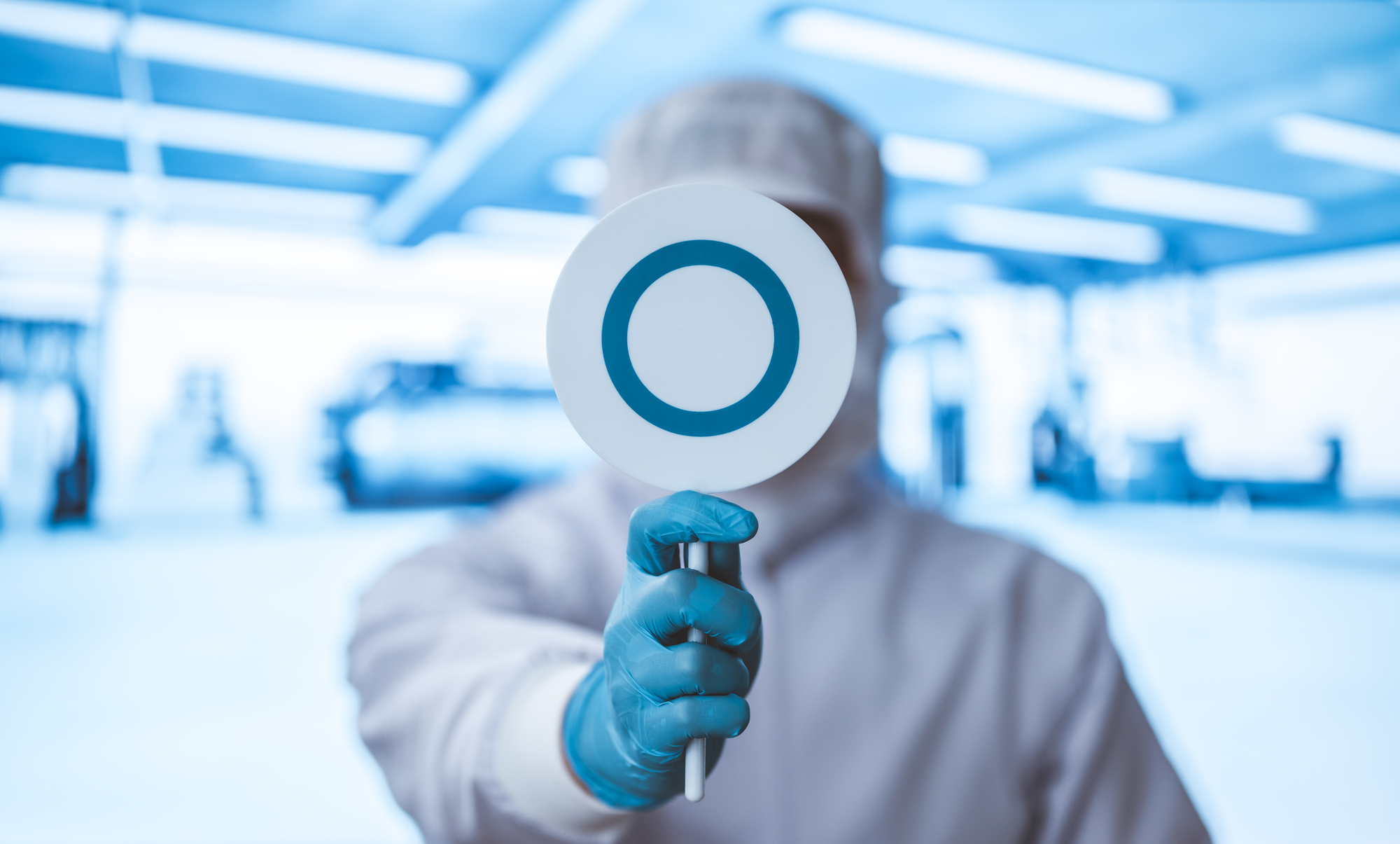
衛生管理区域の優先配置
失敗例
衛生管理区域(清潔区)を設ける際、包装エリアの配置が原材料処理エリアに近すぎたため、原材料の粉塵や湿気が清潔区に流れ込み、製品に影響を及ぼしたケースがあります。また、清潔区のゾーニングに対する考慮が不十分で、作業者の動線が頻繁に汚染区域を通る設計になり、クロスコンタミネーションのリスクが高まった事例もあります。
計画のポイント
衛生管理区域は、**製品が完成形となる最終工程(包装・検査・出荷準備など)**に優先して配置します。原材料処理エリアや廃棄物搬出エリアから十分な距離を取り、間に適切な仕切りやエアロックを設けることが重要です。また、空間を確保できない場合、中間区域を設けて温湿度や空気流れを制御し、清潔区内への粉塵や異物の侵入を防ぐ設計を採用します。
具体的な対策
物理的な仕切りの活用
清潔区は、食品工場専用の飛散防止仕様のパネル材や耐久性に優れた透明プラスチック(ポリカーボネートやアクリル)を使用して仕切ります。これにより、視認性を確保しながら、割れによる混入リスクを排除します。また、仕切りには防塵・防水加工を施し、清掃が容易な構造とします。
1.作業動線の設計
従業員や物品が清潔区を通過する際、汚染区域を経由しない一方通行の動線を設けます。特に、清潔区へのアクセスはエアロック、手洗い・消毒ステーションを通過するルートを必須化します。これにより、逆流リスクを排除し、衛生管理を徹底します。
2.ゾーニングの見直し
設計段階で全体レイアウトを可視化し、清潔区を製品出荷エリアに直結させる配置を検討します。これにより、清潔区内での作業効率が向上し、汚染リスクが低減されます。
3.十分な面積の確保
清潔区には作業人数や設備配置を基にした十分なスペースを確保します。動線が交差せず、従業員が作業しやすい余裕のあるレイアウトを構築します。また、将来的な生産ラインの拡張に対応できる設計も重要です。
4.空調と換気の管理
清潔区は陽圧環境に設定し、隣接エリアからの空気流入を防ぎます。空調システムには、高性能フィルターを導入して粉塵や微生物の侵入を防ぎます。また、定期的な換気と湿度管理で衛生環境を維持します。
食品工場では、飛散や異物混入を防ぐためにガラスを避け、割れにくい素材を使用することが基本です。そのため、設計段階で使用する素材や施工方法を慎重に選定し、安全で衛生的な環境を構築します。
清潔区は陽圧環境に設定し、隣接エリアからの空気流入を防ぎます。陽圧レベルは、清潔区と隣接エリア間で5~20Pa(パスカル)程度の圧力差を確保することが推奨されます。これにより、空気が清潔区内から外部に流れ出す状態を維持し、粉塵や微生物の侵入リスクを低減します。
空調システムには、HEPAフィルター(捕集効率99.97%以上)やULPAフィルターを導入して微粒子を除去します。また、換気回数を24~30回/時(清潔区の基準に応じて調整)に設定し、空気の清浄度を保つ設計とします。
さらに、湿度は40~60%に管理し、結露や菌の繁殖を抑える環境を維持します。圧力、温湿度、換気状態はモニタリングシステムを活用し、リアルタイムで管理することが衛生環境の安定に効果的です。