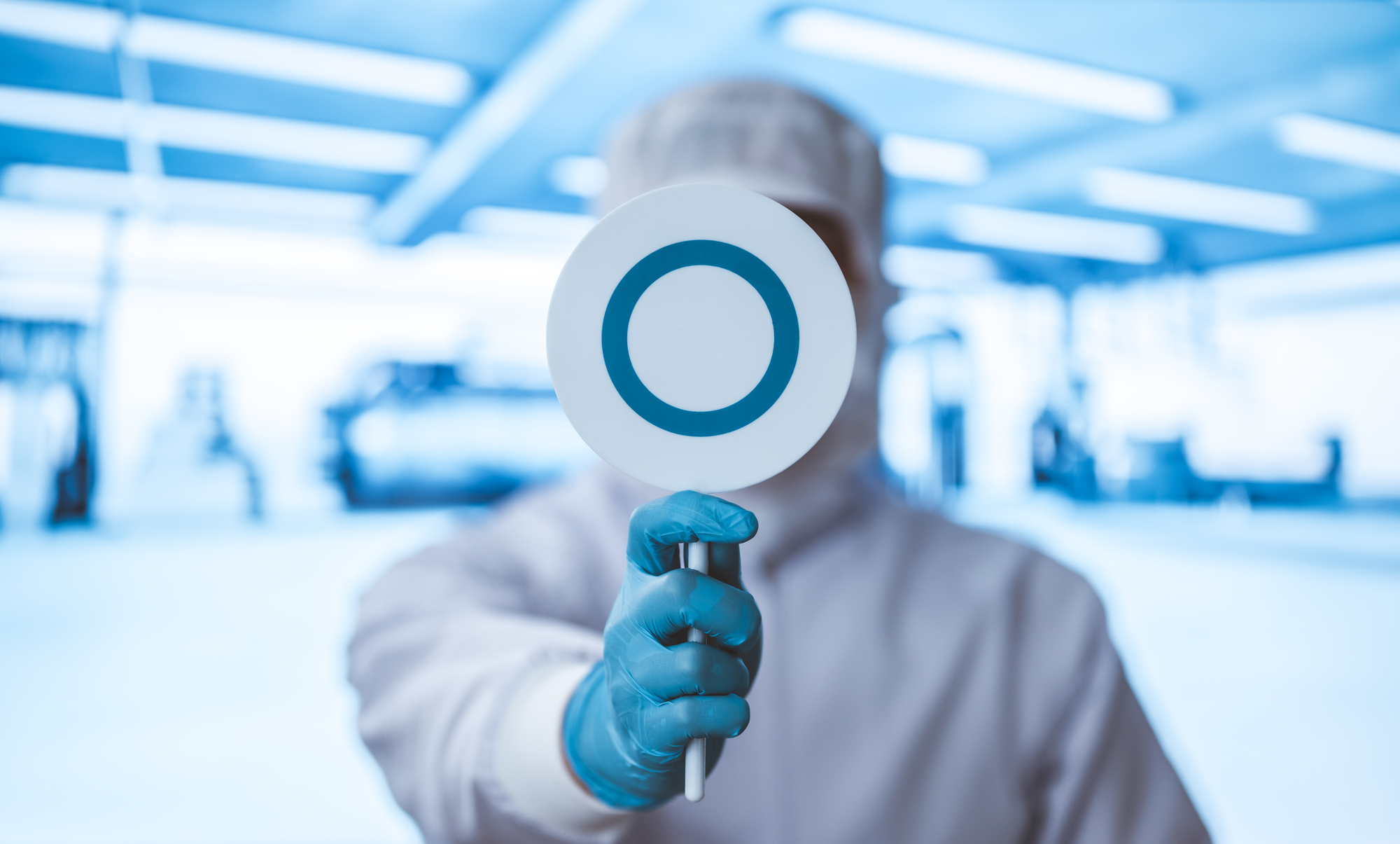
原材料から製品までの動線計画
食品工場の設計において、原材料から最終製品に至るまでの動線計画は、生産効率を最大化し、交差汚染リスクを最小限に抑えるために欠かせない要素です。以下では、動線計画の具体的な方法とポイントを解説します。
1. 動線計画の基本原則
動線計画を立てる際には、次の基本原則を守ることが重要です。
一方向の流れを確保
— 原材料から製品までの流れが一方向になるよう設計し、逆流を防ぎます。
交差汚染を防止
— 人と物、清潔区域と汚染区域の動線が交差しないようにします。
効率的なレイアウト
— 不必要な移動を排除し、作業時間を短縮します。
2. 各工程での動線計画
原材料搬入エリア
原材料は汚染区域で受け入れ、清潔区域に持ち込む前に検査と洗浄を行います。
専用の搬入通路を設け、他の動線と交わらないようにします。
一次加工エリア
原材料を加工しやすい位置に配置し、準清潔区域として動線を分離。
廃棄物の処理動線は製品の動線と独立したルートを設計します。
加工エリア
二次加工や最終加工が行われる清潔区域。
作業者は衛生管理設備を通過してからこのエリアに入る設計とします。
機器配置を最適化し、加工工程がスムーズに進むようにします。
包装エリア
最終製品を清潔な状態で包装する専用のエリアを設定します。
清潔区域内で独立した動線を確保し、汚染区域との接触を防ぎます。
製品出荷エリア
完成した製品は専用の出荷通路を通じて出荷エリアに運びます。
原材料搬入エリアと物理的に分離された設計が重要です。
3. 人の動線と物の動線の分離
人の動線管理
作業員の動線は更衣室や手洗い設備を通るように計画し、清潔を保つ手順を徹底します。
清潔区域へのアクセスにはエアシャワーや消毒設備を設けます。
物の動線管理
原材料、半製品、最終製品の流れを分離し、それぞれ専用のルートを設定します。
汚染物質を含む廃棄物の動線を完全に独立させます。
4. 空間レイアウトと設備配置の工夫
空間利用の最適化
限られたスペースを有効活用し、動線の交差や混雑を防ぎます。
ゾーニング設計と連動させて、効率的なレイアウトを実現します。
設備配置
作業の流れを妨げないように設備を配置し、必要な機器が適切な位置に配置されるよう設計します。
モジュール式の機器配置を採用し、将来的な変更にも対応可能にします。
5. 動線計画の具体例
A社の食品工場例
原材料搬入後、専用の洗浄エリアで一次処理を行い、加工エリアに移動。
各エリア間に衛生管理設備を設け、動線が交差しないよう徹底。
最終製品は包装エリアから直接出荷エリアへ移動し、搬出をスムーズに実現。
6. 動線計画のためのツールと技術
3D設計ソフトウェア
— 工場全体の動線を視覚的に確認し、問題点を事前に解決。
シミュレーション技術
— 人と物の流れをシミュレーションし、効率的な動線を検証。
センサーとIoT技術
— 動線上の混雑や問題箇所をリアルタイムで把握し、改善案を導入。
まとめ
原材料から製品までの動線計画は、効率的な生産と食品安全の確保に直結します。創実ファシリティーズ株式会社では、最新の技術を活用した動線計画を提案し、お客様の工場設計を包括的にサポートします。お気軽にご相談ください。